アルミスポット溶接
アルミスポット溶接技術
環境に優しいエコロジックな接合として普及されているスポット溶接。こだまでは特に車両部品・道路標識・弱電機器部品など、数百種類を超える溶接実績と、板厚t0.1の薄板から筐体のアルミスポット溶接まで、創業50余年幅広く対応してきました。
また、アルミ(A5052)材板厚t0.05~t4.0、筐体奥行750mm(板厚により対応エリアは限定されます)など様々なバリエーションに備えて、アルミ専用の社内製作電極(チップ)を標準装備し実績点数、数十万点以上のアルミスポット溶接加工の実績で板金成形品、アルミ材線材など様々な分野の製品製作及びアルミスポット溶接加工を手がけています。製品実績としては、弱電部品、航空機部品、車両部品(新幹線)、道路標識まで、製品製作に加え安定した強度をご提供しています。
また、アルミ合金においてはジュラルミンと呼ばれる2000番台の溶接は避けれることが多いですが、弊社では多様なノウハウからジュラルミンのスポット溶接にも対応可能です。
※アルミのスポット溶接時には非常に大きな溶接出力が必要です。そのためゴミなどの不純物がある場合には爆飛するなど非常に危険なため、溶接面は清浄である必要があります。また、アルミの表面は酸化しやすい材料です。表面が酸化している場合には溶接電流が流れにくい、または流れないため溶接不良を起こす可能性がります。そのため、溶接する際には材料管理も非常に大事な要素となる金属です。
※航空宇宙用スポット溶接のJIS規格であるAWS A 3.0(MIL規格のW-6858Dに相当)の基準値をクリアできる設備でスポット溶接しております。
最近では精密なアルミのスポット溶接も増えてきました。左上の画像左下のスポット溶接箇所のスポット溶接可能な範囲は7mm程度しかありませんが問題なく溶接できています。溶接しろが5mm程度でもアルミのスポット溶接可能ですが、母材と母材の隙間からバリや溶け垂れが飛び出てしまう可能性が高いです。また、スポット溶接痕が美観上キレイなことも利点の一つです。
![]() 車両部品のアルミスポット溶接 |
![]() モニターテレビのアルミスポット溶接 |
![]() アルミケースのスポット溶接 |
![]() 産業機器のアルミスポット溶接 |
![]() アルミ線材のスポット溶接 |
![]() 産業機器のアルミスポット溶接 A5052 t1.0 3枚重ね |
![]() 道路標識 アルミスポット溶接 |
![]() 道路標識 アルミスポット溶接 |
![]() 反射板 アルミスポット溶接 |
※アルミスポット溶接の加工事例は、こちらから
※その他材質のスポット溶接事例は、こちらから
※スポット溶接できる材質については、こちらから
「こだま」が、ご提供できること
t0.05~t4.0のアルミスポット溶接
- 1,各種溶接の受託加工
- 2,冶具電極の設計・製作(こだま社内用)
- 3,試験、溶接条件販売、スポット溶接機の選択・販売支援
- 4,秘密保持契約
- 5全国対応
試作について
「こだま」では創業50余年で蓄積した抵抗溶接ノウハウ・各種治具電極製作を活かし、様々な素材・形状および材質に対応した試作・開発を行っています。
![]() ハイテン材抵抗スポット溶接試作 |
![]() アルミ合金抵抗スポット溶接試作 |
![]() 抵抗スポット溶接試作 |
![]() 銅より線んとステンレス板の 抵抗スポット溶接試作 |
![]() ハイテン材と袋ナットの プロジェクション溶接試作 |
![]() 熱電対のレーザースポット溶接試作 |
スポット溶接とは
スポット溶接とは、溶接したい2片の金属母材を上下から電極で挟み込み接触部を電極で加圧します。
加圧した電極より金属母材へ大電流を流すことにより電気抵抗によるジュール熱を発生させ、局部的に発熱・溶融させる抵抗溶接の一種です。
スポット溶接は、抵抗溶接機にプラテン部分にホーンという、いわば機械の腕にあたる真鍮(一般的に使用されている)の無垢材を取り付け、先端に電極を取り付けたホルダーを固定して使用します。電極は、ストレートタイプ、エルボタイプ、または自作の特殊なものまで、被溶接材に合わせて、最適なものを選択します。また、高出力の機種では、アルミ合金等の非鉄金属の溶接が可能です。
![]() |
![]() |
スポット溶接の特徴
長所
①溶接時間が短いので、他の溶接方法(抵抗溶接以外)に比べ加工コストが極めて低い。
②短時間で溶接が出来るので、加熱域が溶接部近傍に限られるため、被溶接材の熱歪が少ない。
③機械的作業のウエイトが高いため、一般的な製品の溶接においては、作業者の熟練度をほとんど必要としない。
④溶接棒やフラックスが不要で、有害な紫外線やヒュームが発生しない。
⑤機種と電極の選択で、t0.03~の金属板、金網(メッシュ)、線材、鉄、非鉄金属等、幅広い範囲での溶接が可能。
短所
①大きな電流が必要なため、溶接機および受電設備の電気容量が大きくなる場合がある。
②機種にもよるが、溶接機の価格が比較的高い。
③被溶接材に対し、機種の選択が必要となり、溶接電流、通電時間、加圧力、電極形状などの溶接条件を、
被溶接材の材質や板厚ごとに選定する必要がある。
④接合状態を外観から判定しにくく、判断基準を設けるには熟練度が必要となる。
※高い判断基準が設けることが出来れば、大量生産においても安定した溶接が望める。
アルミ材におけるスポット溶接
アルミ(アルミニウム)は、耐食性がよく一般の鋼材と比較して、熱膨張係数が約2倍、凝固収縮率は約1.5倍、熱伝導率も約4倍と、ティグ溶接等においては熱歪が生じやすい素材です。また、素材表面には空気中に生成された薄い酸化膜があり、スポット溶接においては、その材料特性を把握しておかなければ、良好なナゲット(溶け込み)がえられません。また、アルミ材は電気抵抗値が低くジュール熱が発生しにくい上に、表面の酸化被膜がありますので、その酸化皮膜を突破し、大電流を流す必要があります。ですので一般的なスポット溶接機では無く、出力が高く適切な加圧を掛けれるスポット溶接機が必要となります。しかし、上記特質の把握と、溶接条件を満たしてさえいれば、高い溶接強度の安定性と、生産性がえられます。
スポット溶接におけるアルミ材の注意点
①電気抵抗が小さく、熱伝導が大
②アルミと電極の銅とが合金しやすく、電極表面の汚れが生じやすい
③材料表面に酸化膜があり、接触抵抗との係わり合いが大きい。
④ナゲット生成前後において、塑性範囲が狭いので、供給エネルギー(溶接電流及び通電時間)の
精密な制御が必要である。
⑤膨張係数が大きく(南港の2倍強)、溶接中のナゲット形成においてガスを吸蔵しやすく、
ナゲットの凝固過程において、収縮割れや気泡を生じやすい。
①に関しては、同一電流を流しても発熱は小さく発生した熱は逃げやすく、アルミと軟鋼を比較すると抵抗は常温で約1:6、溶融点は約1:15と開いていて、反対に熱伝導は約5:1です。
そのため同一板厚にお対しても、アルミは軟鋼の場合の3倍強の溶接電流を必要で、電気入力(KVA)としては約10倍の電流を必要とします。
抵抗スポット溶接の品質要因
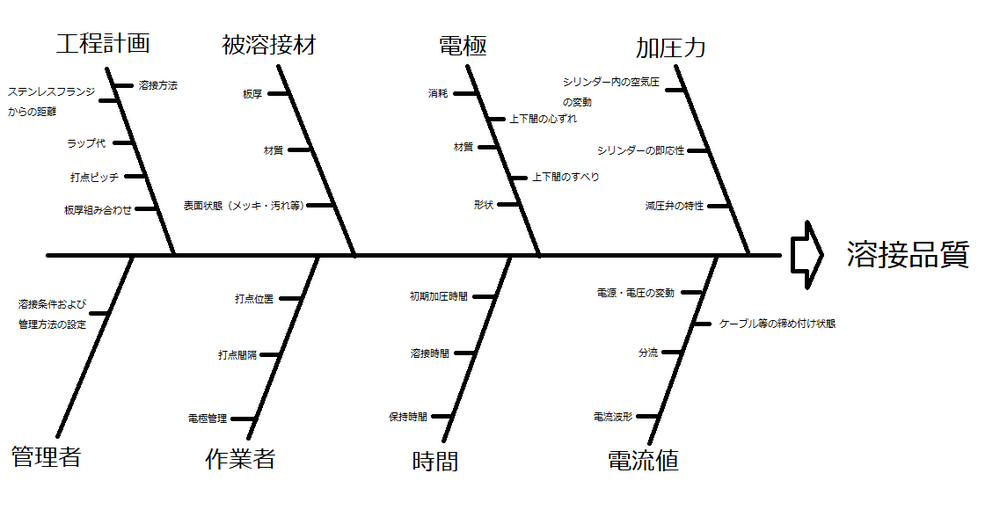
スポット溶接の四大条件
※アルミ材のスポット溶接の他、一般的な視点を交えて解説します。
1)加圧力
溶接したい2片の金属母材を、上下から電極で挟み込み接触部を電極で加圧し、電流を流すことで、
スポット溶接を行いますが、その加圧が溶接箇所の安定性に繋がります。
加圧は、材質・板厚によって異なります。
2)溶接電流
溶接電流は、母材を局部的に溶かすための要素となります。
アルミ材のスポット溶接は、他の材質と比較して、表面の酸化被膜を溶かすために、
高電流が必要となりますが、電流値としては、低いと溶接外れの原因となりますし、
高すぎると、ナゲットの極端な凹みが生じて、スポット溶接後の母材強度を損ねてしまいます。
また、アルミ材のスポット溶接では、母材・電極に異物の除去は必ず行わないと、
通電時に、高音と同時に、母材に穴があくほどの爆火が生じます。
3)通電時間
溶接電流を流す時間を指します。
溶接電流とのバランスで、より安定したアルミ材のスポット溶接のナゲットを形成します。
4)電極
アルミ母材の板厚が、電極サイズの基準になりますが、スポット溶接を行う場所のスペースに
よって合わせる必要性が生じてしまいます。
上記の「爆火」に気を付けることの他、
スポット溶接という、合理的接合の反面、外観上はナゲットでしか確認できない為、
作業においては、熟練度を要します。熟練の判断があれば、安定したアルミスポット溶接が可能です。
①電極
-
材質:一般的にはクロム銅が使用されています。
-
形状:被溶接材の形状、板厚などに合わせますので、様々な形状があり、ほとんどが、市販されています。
|
|
②電極形状
一般的には、電極先端に切削加工等でR形状に仕上げたモノを使用しますが、方側が外観面になるなど、
スポット溶接による"くぼみ"を軽減したい場合は、外観側の電極は平面処理を行い、
反対側の電極先端はR形状に、仕上げたモノを使用します。
なぜ、電極は被溶接材と一緒に溶接されないのか
材質の導電性が高く、電気抵抗値が低いクロム銅等を使用しているからです。
(電気抵抗値が低いと通電時の発熱が少ないためです。)
③冶具・電極(位置決めについて)
2点以上被溶接材をスポット溶接する時、部品の位置決め等が必要ですが、被溶接材を外部的に固定する場合には、
冶具に電極を挿入した冶具電極を製作する必要があります。
また、被溶接材にダボ(凸)と、穴(凹)を施した位置決め方法があります。
治具を製作する場合にはイニシャルコストが上がり、ダボ穴を施工する場合より
費用が掛かります。また、加工時にも手間が掛かることが多いため加工費用も上がる可能性が有ります。
![]() 冶具電極 |
![]() 被溶接材のダボ穴(凸凹) |
④被溶接材に対する加圧の設定
加圧は、通電を行って被溶接材にナゲットが生じだしたときに、ちりの抑制とナゲットの状態を安定させるための
役割と、通電後、溶接部を加圧しながら冷却することによって、ナゲット内の欠陥を減少させます。
⑤溶接電流と通電時間の設定
溶接時間とのバランスを取りますが、まず、基準値が無い場合には、低い電流設定から徐々に上げていく、
手順を行います。危険ですので間違っても上げ過ぎには、注意が必要です。
通電時間も、低い設定値から上げていきますが、ナゲット面積を大きくしたい場合には、
設定値を大きくします。その分溶接電流は最終規定値より下がる方向性です。
溶接された時点で、被溶接材の剥離検査を行いながら、強度確認を行い適切な溶接電流値
通電時間を設定を行います。
⑥溶接強度テスト
専用の引っ張り試験機を使用すれば、正確な強度数値も得られますが、一般的には、
被溶接材の剥離テストを行い、適切な溶接条件確認から、溶接回数に対しての定期的なテスト基準値を設け、
電極管理につなげることで、溶接強度の安定性を高めることが可能です。
よって、溶接強度テストは、最適な溶接条件と共に重要項目となります。
引っ張り試験機 |
工具を使用した、簡易的な剥離テスト |
剥離テスト後 |
スポット溶接条件設定のフロー |
1)溶接箇所の検討 |
2)⇒電極形状の決定 |
3)⇒加圧の選定 |
4)⇒溶接電流・通電時間の選定 |
5)⇒溶接テスト⇒剥離検査⇒溶接条件の調整 |
6)⇒加圧の決定 |
7)⇒溶接電流・通電時間の決定 |
8)⇒試作⇒量産試作 |
9)⇒品質管理項目の策定(量産条件の決定) |